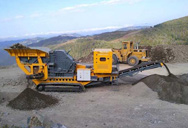
MIDREX® Process - Midrex Technologies, Inc.
2023年10月19日 The shaft furnace is where iron ore is converted to metallic. Iron oxide, in pellet or lump form, is introduced through a proportioning hopper at the top of the shaft
Consulter un spécialiste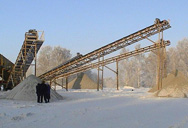
Modeling and Simulation of the MIDREX Shaft Furnace:
2015年8月21日 There are several technologies, like MIDREX1 and H.Y.L2 using the countercurrent shaft furnace to make sponge iron. In MIDREX technology, the furnace is
Consulter un spécialiste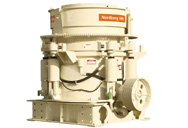
在MIDREX 工艺中用合成气生产直接还原铁
2021年7月8日 内容 使用煤的直接还原 MXCOL®(发音为“M-X-COAL”)是成功商业化的MIDREX®直接还原工艺名称和商标,使用从煤制取的合成气. 合成气是含碳燃料气化后产
Consulter un spécialiste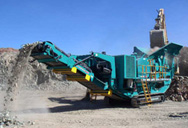
Design Shaft Furnace (Mt/y) ModulesStart-up Product
2021年12月10日 SINCE 1969, THERE HAVE BEEN NEARLY 100 MIDREX® SHAFT FURNACE DIRECT REDUCTION MODULES BUILT AROUND THE WORLD. MIDREX®
Consulter un spécialiste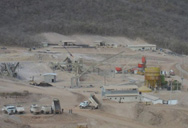
Modeling and Simulation of the MIDREX Shaft Furnace:
2015年8月21日 MIDREX technology which is the most important gas-based direct reduced iron (DRI) process in the world, includes reduction, transition and cooling zones. The
Consulter un spécialiste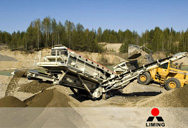
Shaft Furnace Direct Reduction Technology -
Midrex and HYL Energiron are the leading technologies in shaft furnace direct reduction, and they account for about 76% of worldwide production. They are the most competitive ways to obtain high quality direct reduced
Consulter un spécialiste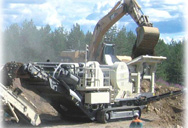
Modeling and Simulation of the MIDREX Shaft Furnace:
2015年8月21日 The focus of this study is to simulate the furnace of the MIDREX technology. MIDREX technology which is the most important gas-based direct reduced
Consulter un spécialiste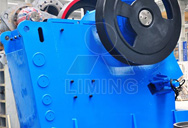
Shaft Furnace Direct Reduction Technology - Midrex and
2013年9月1日 MIDREX, HYL, and Energiron are some of the processes based on shaft furnace (Béchara et al. 2018; Jiang et al. 2013; Patisson and Mirgaux 2020). These days
Consulter un spécialiste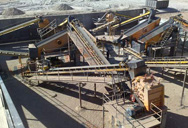
Overview of the MINIMOD ® MIDREX shaft
Overview of the MINIMOD ® MIDREX shaft furnace (left) and view of the simulated sections (middle and right). The number of particles corresponded to the 25 mm spheres simulated in each section.
Consulter un spécialiste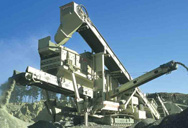
Modeling and Simulation of the MIDREX Shaft Furnace:
2015年8月21日 Request PDF Modeling and Simulation of the MIDREX Shaft Furnace: Reduction, Transition and Cooling Zones Metallic iron used in steel industries is mostly
Consulter un spécialiste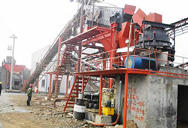
Hydrogen Direct Reduced Iron SpringerLink
2022年4月20日 Thus, the MIDREX ® Process has successfully produced DRI at H 2 /CO ratios from 0.37 to 3.8. Based on initial modeling and laboratory experiments, it is possible to use almost pure hydrogen to make DRI in a MIDREX ® Shaft Furnace (Fig. 13).
Consulter un spécialiste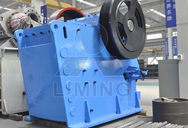
Development and Progress of Hydrogen Metallurgy
2021年4月27日 Ironmaking Technology in the US, HYBRIT in Nordic, Midrex H 2 TM, H2FUTURE of Voestalpine, SALCOS Project of Salzgitter. The hydrogenrich BF with COG injection is typical in China. ... coal gasification-gas based shaft furnace with an annual output of 10,000 t DRI was under construction. The reducing gas of 57%H 2 and 38%CO
Consulter un spécialiste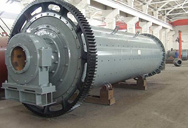
WORLD DIRECT REDUCTION STATISTICS - midrex
2023年9月12日 1990 2000 2010 2022 Year MIDREX® Other Shaft Furnace Total Shaft Furnace DRI Production by Process and by Year 91.68* Mt 199010.73 15.98 5.25 199111.96 17.36 5.40
Consulter un spécialiste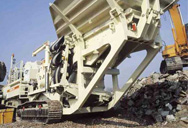
氢冶金的发展现状与进展 - USTB
2020年5月22日 The life cycle of the coal gasification–gas-based shaft furnace–electric furnace short process (30wt% DRI + 70wt% scrap) is assessed with 1 t of molten steel as a functional unit. This plant has a total energy consumption per ton of steel of 263.67 kg standard coal and a CO 2 emission per ton of steel of 829.89 kg, which are superior to
Consulter un spécialiste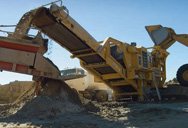
Shaft furnace technologies related to materials and
Shaft furnaces based on the counter flow principle are widely used in steel and foundry industries as well as in non-ferrous metallurgy, e.g. blast furnace, Midrex, Corex, OxiCup furnace, cupola furnace or Imperial smelter. To keep and to enhance advantageous of the shaft furnaces as ideal counter-current reactors, research activities at Dept.
Consulter un spécialiste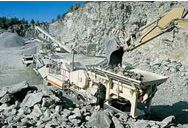
Direct Reduced Iron: Most Efficient Technologies for
2019年7月19日 The proper oxygen blowing position is at the height of 6.5 m, the inlet gas flow rate is 37,083 Nm 3 /h, and the oxygen flow rate is 536 Nm 3 /h for the studied shaft furnace. Compared with the traditional MIDREX furnace, the carbon emission will decrease by 26.9%, and the energy consumption will decrease by 19.6% with oxygen blowing.
Consulter un spécialiste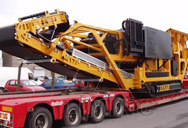
Technoeconomical investigation of energy harvesting from MIDREX ...
2022年1月15日 In Midrex reformers which equipped with nickel catalysts, the shaft furnace top gas reacts with methane to produce a reducing gas which is rich of CO and H 2 [10]. Feeding the mixture of the reductants to the shaft furnace reduces the iron oxide pellets or lumps (Fe 2 O 3) into metallic iron which is discharged from the furnace [10]. From heat ...
Consulter un spécialiste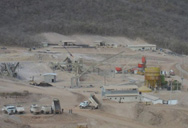
Report : MIDREX direct reduction technology and Arab steel
2021年7月4日 Despite the COVID-19 pandemic that was declared towards the beginning of 2020, MIDREX® Plants produced 65.7 million tons in 2020, 3.0% less than the 67.7 million tons produced in 2019. The production for 2020 was calculated from the 35.5 million tons confirmed by MIDREX Plants located outside of Iran and the 30.2 million tons for
Consulter un spécialiste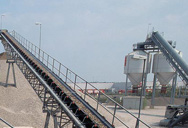
Decarbonisation and hydrogen integration of steel
2023年2月14日 There are different processes/technologies used for DRI production, such as shaft furnaces, rotary kilns, rotary hearth furnaces and fluidised bed reactors. However, as seen in Fig. 5 a, 96.8% of the DRI is produced using shaft furnace technology (72.4%) and rotary kiln (24.4%) (MIDREX, 2020). Download : Download high-res image (386KB)
Consulter un spécialiste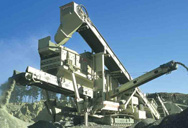
1, ,†, Jose Barros 2, Pascal Gardin 2 - MDPI
2021年12月4日 a blast furnace and to establish prospective operating points for optimization [7,10–13]. The more-recently developed Midrex NGTM and Tenova HYL processes have strong similarities with the blast furnace. The reduction shaft furnace can also be thought of as an oxygen exchanger in a counter-current gas–solids reactor
Consulter un spécialiste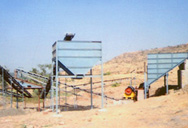
[Great Conversion to Low-carbon Eco-friendly
2022年6月2日 A shaft furnace uses pellets, iron ore that was crushed and screened and then processed in a round shape with a certain size, while a fluidized bed reduction reactor uses iron ore fines, which is just mined
Consulter un spécialiste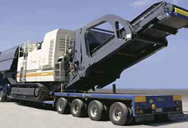
Metals Free Full-Text Adaptation of the Rist
2021年12月4日 The blast-furnace operating diagram proposed by Rist was revised to direct reduction and was specifically applied to the Midrex NGTM process. The use of this graphical tool in the study of an industrial
Consulter un spécialiste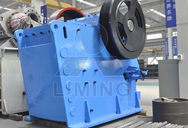
DEVELOPMENT OF A DOUBLE LAYER LINING FOR DRI
2023年11月20日 According to the statistics of MIDREX (2013), from the global production 78,6 % is of total DRI is generated in shaft furnaces, MIDREX, HyL and ENERGYRON, while the productions of DRI in rotary ...
Consulter un spécialiste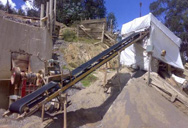
Pressurized Chemical Looping for Direct Reduced Iron
2022年7月19日 1.2.1. Shaft Furnace The shaft furnace is the heart of the DRI process. Iron ore (usually in pellet form) is fed to the top of the furnace, while reducing gas is fed from the side and flows counter-currently to the ore. The reducing gas enters the furnace at 850–900 C for Midrex or 920–1050 C for Energiron III [12].
Consulter un spécialiste
Towards fossil-free steel: Life cycle assessment of biosyngas
2023年3月20日 The subsystems consist of a biomass dryer, a gasifier, a tar reforming process, a DRI shaft furnace (similar to the MIDREX furnace), and a CO 2 removal process, as presented in Fig. 1. The key component of the direct reduction process is a shaft furnace, where the reduction of iron ore to DRI by using biosyngas or other gaseous reducing
Consulter un spécialiste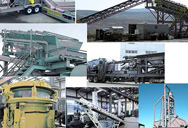
Modeling and Simulation of the MIDREX Shaft Furnace:
2015年8月21日 Metallic iron used in steel industries is mostly obtained from a direct reduction process. The focus of this study is to simulate the furnace of the MIDREX technology. MIDREX technology which is the most important gas-based direct reduced iron (DRI) process in the world, includes reduction, transition and cooling zones. The
Consulter un spécialiste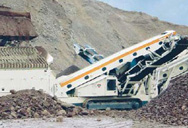
Influence of the ReducingGas Distribution in the Tuyere
2017年8月26日 the refractory lining in shaft furnaces that arise on account of fluctuations in its operation [1]. The pro ductivity of shaft furnaces of reduction type depends primarily on the temperature of the reducing gas sup plied. Therefore, operation at the maximum possible temperature without caking is advisable [2].
Consulter un spécialiste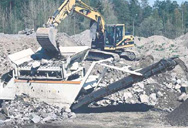
Detailed Modeling of the Direct Reduction of Iron Ore in
2018年10月9日 the blast furnace, basic oxygen route [2]. Among DR processes, shaft furnaces represent over 82% of the world’s DR iron production, with the two main processes being MIDREX (65%), as shown in Figure 1, and HYL-ENERGIRON (17%) [3]. In a DR shaft furnace, a charge of pelletized or lu mp iron ore is loaded into the top of the furnace
Consulter un spécialiste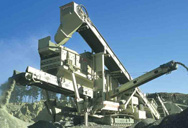
(PDF) Hydrogen Ironmaking: How It Works - ResearchGate
2020年7月9日 of a MIDREX shaft furnace using different H 2 /CO ratios at the reducing gas inlet [27]. Figure 10 shows that the higher the H 2 content is, the lower the metallization degree of the DRI, which at ...
Consulter un spécialiste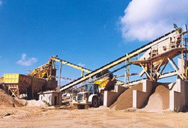
Cost Effectiveness Analysis of HYL and Midrex DRI
2016年4月27日 the shaft furnace, it can be cooled and compressed to briquetted iron for safe storage and transportation. The hot metal can also be taken directly to the electric arc furnace for immediate use. This technology eliminates the need for a coking or sintering plant. (Industrial Technology Database, 2012). A process flow
Consulter un spécialiste>> Next:Valeur Standard De Densité De La Roche